|

4 Myths You Believe About Mass Timber Construction That Just Aren’t True
What makes MT a realistic material for building a modern, state-of-the-art data center is prefabrication and the ability to utilize hybridization – leveraging the best traits of each assembly by combining the speed and flexibility of MT with the advantages of steel.
​
Prefabricated MT is designed and built offsite, transported to your build site, and assembled onsite. This is the key because it takes much risk and guesswork out of the equation, streamlines efficiency, and shaves an eyebrow-raising chunk off the price tag.
Myth #1:
Mass Timber is More Expensive than Steel & Concrete.
Comparing merely the price of lumber versus the price of steel and concrete is like comparing apples and oranges when cost-estimating your data center build. You must look at the entire project, from concept to commissioning, to get a true comparison of the cost difference between steel and concrete versus Mass Timber. With all things accounted for, Mass Timber generally comes out the winner in terms of the overall ROI.
​
When you have an entire team of specialists working in concert from the design phase through the final assembly process, the cost savings are significant, shaving 30% off the timeline by expediting construction activities via prefabricated solutions and schedule efficiencies and reducing cost through reduced general conditions and field labor expenditures; thus, hyperscalers can bring energization and lease-start dates forward.
Myth #2:
Mass Timber is More of a Fire Risk than Steel & Concrete.
Mass Timber differentiates itself from light frame wood by its inherent volume of wood fiber such that the elements char in a fire event rather than rapidly combust. Relate it to trying to start a campfire by trying to ignite a large log to start. CLT is the first wood product to natively achieve a Class A flame spread rating.
​
MT buildings are protected from many fires due to the char factor. When exposed to heat, wood chars, essentially sealing the wood from the ignition source. It can take hours for the wood to finally ignite under these circumstances, and modern fire detection and protection warn workers in ample time to correct the situation before this happens.
​
So, as counterintuitive as it seems, Mass Timber, especially in a hybrid build, can be more resistant to fire than a purely concrete and steel structure.
Mass Timber Fire Testing Video
Myth #3:
Mass Timber Construction is No Faster Than Steel & Concrete.
On-site construction is fraught with potential impacts only a sophisticated design-build team can mitigate with creative schedule coordination. Conventional on-site construction methodologies compound weather impacts (topping slab cure is one such example). It is difficult to obtain the volumes of skilled labor when (and where) needed. Then, there are safety concerns, logistical issues, and delays in getting materials and equipment delivered on time. You simply can’t control all of the elements in an on-site build.
​
Prefabrication minimizes the need for a large on-site skilled labor force by shifting certain jobs — layout, CNC programming and milling, and pre-installed connecting hardware— to a controlled factory environment. The necessary building facilities, workforce, and supply chains are already in place and waiting to be leveraged.
​
Avoiding delays from weather, natural disasters, or other events can save time and reduce costs. With global supply chains affected by geopolitical issues, using locally sourced materials helps minimize the risk of delays from product shortages or logistics challenges. This approach offers greater reliability in project completion.
Myth #4:
Mass Timber Construction is Just as Disruptive to Neighborhoods as Standard Construction Methods.
Prefabricated MT mitigates many negative effects on communities. By building offsite, the length of time communities are disrupted by heavy equipment, and teams of construction workers are significantly reduced. Elements of the data center are brought in ready for fast, efficient assembly with minimal heavy equipment.
-
The number of trucks required to transport MT panels, multi-trade racks, and other off-site fabricated assemblies is notably less than that required for the same project built by conventional means.
-
Site parking, job shacks, material staging, and laydown areas are more compact, and the overall construction footprint is less disruptive to neighbors.
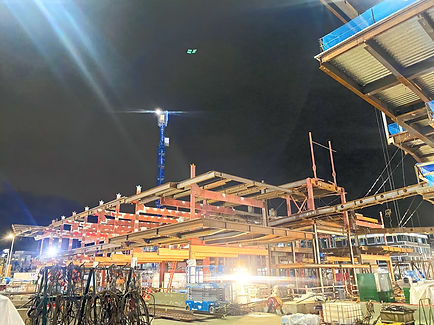
Mass Timber-Steel Hybrid Example