|

Potential Challenges in Mass Timber Data Center Construction
But … Aren’t there any downsides?
​
Absolutely. Everything in life has a downside, and prefabricated MT has its share. Here are the most common obstacles you’ll face and how to mitigate these for inevitable success.
Potential Challenge #1: Inexperienced Design-Build Team
Inexperienced design teams routinely fail to develop a truly efficient design, and contractors will often add extra “contingencies” to their budgets to cover what they don’t know. As such, many potential Mass Timber projects die (or are converted back to steel and concrete) without ever even being fully explored. When selecting the team for your project, make sure everyone has real experience with MT projects, not just the architect and engineering firms, but also your owner’s representative, MT supplier, steel fabricator, MEP installer, erector, and every other trade that will be involved. Doing so not only reduces the risk of issues but will increase budget accuracy and improve the final resulting build.
Having the right team onboard early will help minimize all other risks, including the following:
Potential Challenge #2:
Moisture Management During Construction Process
Unlike concrete and steel, MT is both a structural element and a finished material. It can look beautiful! However, care must be taken during the construction process to ensure it stays that way. Specifically, projects require robust moisture management plans to deal with rain and other moisture until the building is dried in (and to control the change in humidity as the HVAC comes online). Owners should consider specifying factory-applied initial sealers, moisture membranes, and/or protective wraps on the timber elements. Still, care must be taken not to allow water to pool or run onto the timber, or you may find yourself dealing with extensive sanding / refinishing efforts to remove watermarking & rust stains. Such remediation can easily negate all schedule and budget savings that would otherwise have been realized on a project.
NOTE: Even with careful protection, MT is still ultimately structural wood, produced out of large volumes of structural boards and not furniture-grade veneers. Owners and architects should expect to see natural color variation, knots, and checking/cracks.
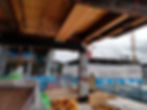

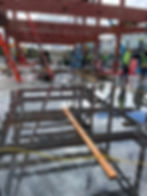
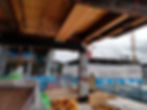
Gallery of Moisture Management-related images.
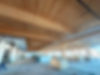
Potential Challenge #3: Jobsite Logistics
While prefabrication can reduce on-site construction schedules, accelerated schedules require careful planning and coordination. Specifically, MT projects benefit from having sufficient laydown space to receive deliveries in bulk, ahead of when they’re required. Alternatively, it’s possible to arrange a “just-in-time” delivery and install directly off the trucks, but that comes with the additional risks of delayed trucks due to any of a number of reasons. If onsite space isn’t available, consider finding a local laydown yard for short-term staging of critical components for just-in-time last-mile delivery.
​
Hybrid buildings require enhanced trade coordination for crane operations (especially with the introduction of prefabricated MEP components). In some cases, multiple cranes may be required to fully realize schedule savings.
​
Additionally, Timber-to-Steel and Timber-to-Concrete connections require close coordination between trades to ensure the scope is captured appropriately, tolerances are accounted for, and on-site steelwork does not damage or discolor wood elements.
Potential Challenge #4: Regulatory & Underwriting Hurdles
Early adopters commonly incur new risks already addressed with conventional methods - for instance, you may find that your local regulatory agencies or insurance underwriters are unfamiliar with MT. However, by partnering with the right allies, you’ll have assistance in navigating through these challenges. Besides your chosen team of experts, agencies such as WoodWorks and the American Wood Council have staff dedicated to helping educate regulatory officials and others.